摘 要:隨著我國航空航天事業的飛速發展,精密鈑金件的應用日益廣泛,根據不同的設計及應用要求,航空管材類零件也由原來的自由脹形工藝逐步改進為各類可控脹形工藝,大大提高了航空管材件的應用范圍。其中,內高壓脹形工藝是廣泛應用于航空制造領域的金屬成形工藝方法之一,成形難度大,影響因素復雜,一直是成形領域的難題。以航空用某卡箍類零件為例,對影響內高壓脹形工藝的軸向材料補償量、內壓力、加載路徑等因素進行深入研究,通過數值仿真分析,優化工藝參數,提出一套簡單易行的管材軸向壓力內高壓脹形工藝方法,成功應用于該類零件的工程實踐中,達到了縮短生產周期、節約生產成本的目的。
來源:《航空制造技術》2018年18期
作者:董楹,黑東盛,白艷
內高壓脹形工藝使金屬毛坯或成形件的局部區域產生變形,通過表面積增大面獲得有凸出形狀零件的沖壓加工方式。這類成形的主要優勢在于可以獲得表面質量好,回彈變形小,相對結構重量較輕,高精度的零件。
從20世紀70年代末德國開始內高壓成形的基礎研究,90年代初德國、美國汽車公司開始在多個車型上應用了內高壓成形的零件,目前該成形技術已廣泛應用于汽車、航空等機棫制造領域的實際生產中。 Tseng等通過數值仿真模擬了板材液壓成形過程中各因素 (包括施加力摩擦力、背壓情況、毛坯尺寸等)對成形討程的影響,并進行了試驗對比,仿真結果與試驗結果相吻合。
以下是正文:
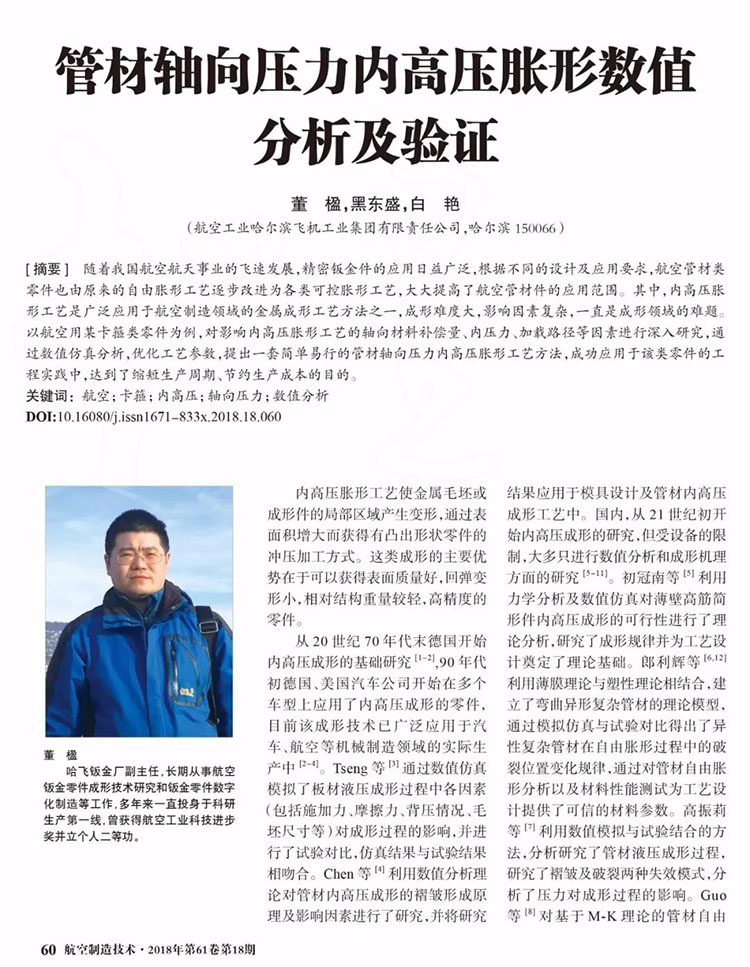
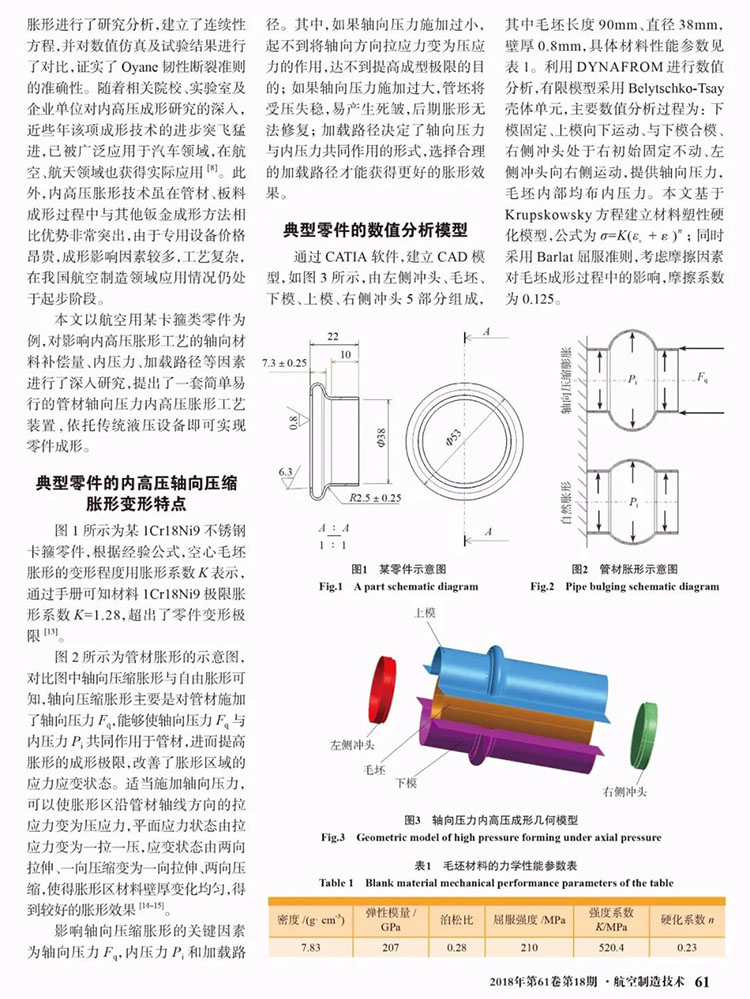
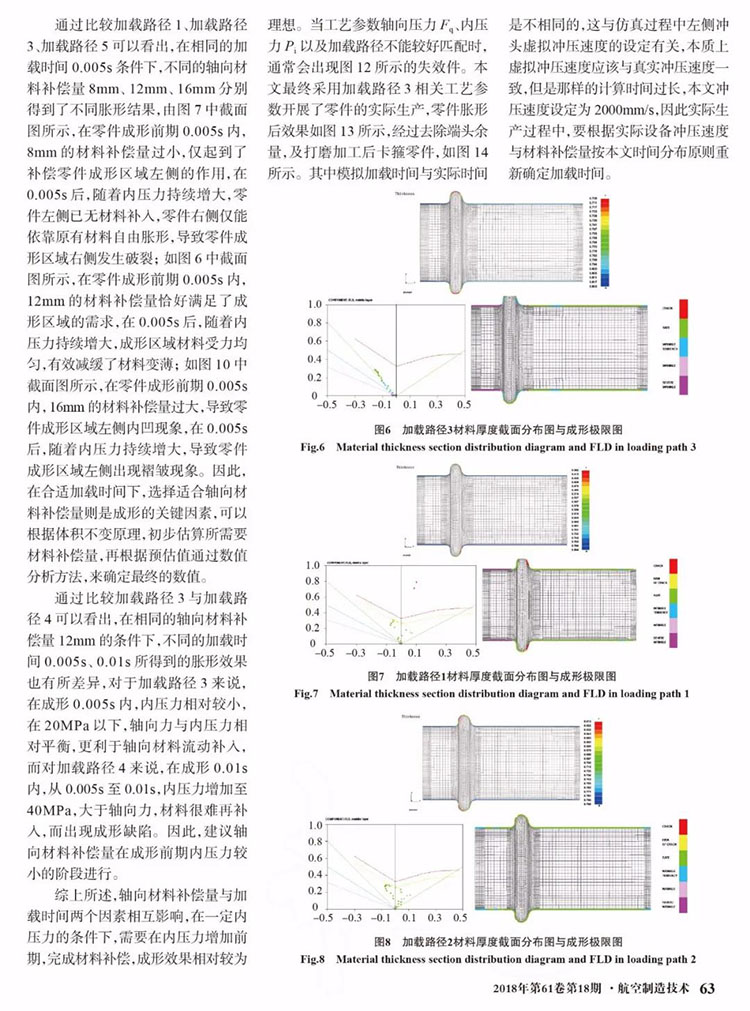
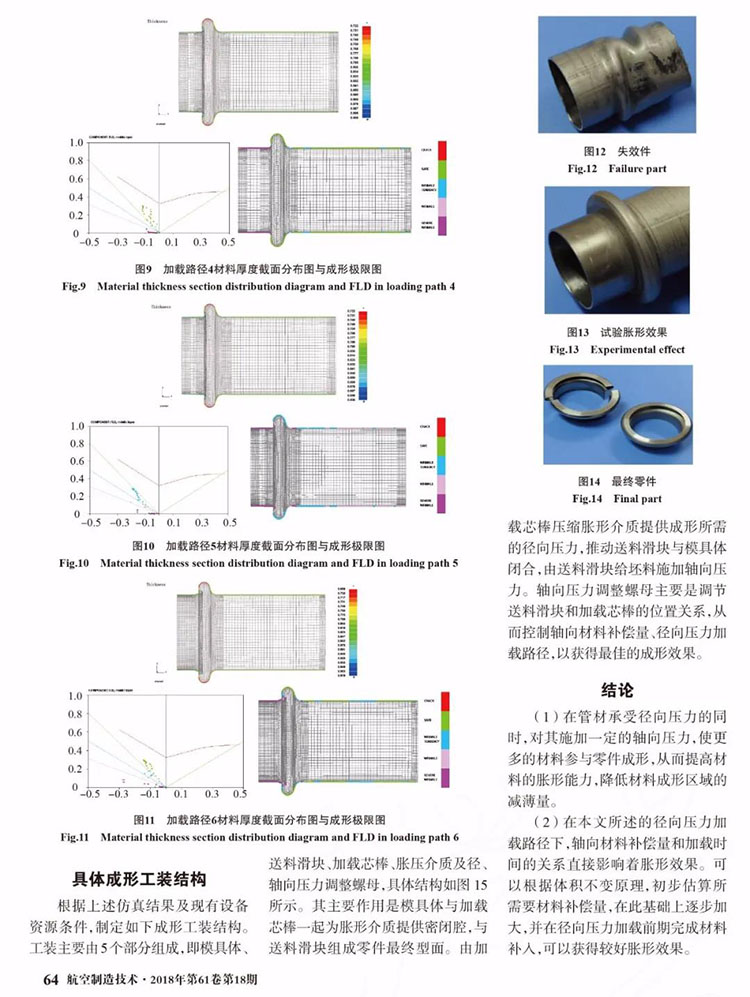
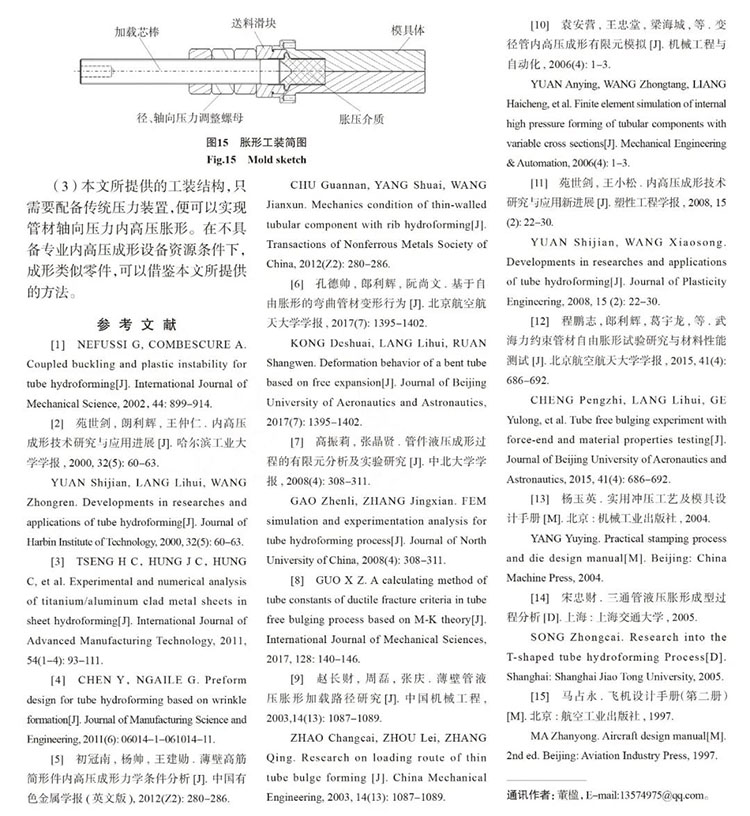